“Anodizing Aluminium” Anodized aluminium and the special properties of different oxide thicknesses
Anodizing is a long-standing technology for finishing aluminium, using an electrochemical process to create an Aluminium Oxide (oxide layer) of varying thicknesses on the aluminium surface. Color is then added to the porous layer created by the anodizing process, and the surface is sealed again, ensuring the color becomes an integral part of the workpiece. Anodizing aluminium is known for its durability, resistance to peeling, and scratch resistance.
The durability of anodized aluminium partly depends on the thickness of the oxide layer. Choosing the appropriate oxide layer thickness according to the product’s application will ensure the workpiece has the desired quality and environmental resistance.
Oxide Thickness up to 10 Microns:
This aluminium has a relatively thin oxide layer, which provides less resistance to weather conditions or chemicals compared to thicker oxide layers. It is suitable for decorative aluminium furniture or electronic devices where thinness and light weight are desired.
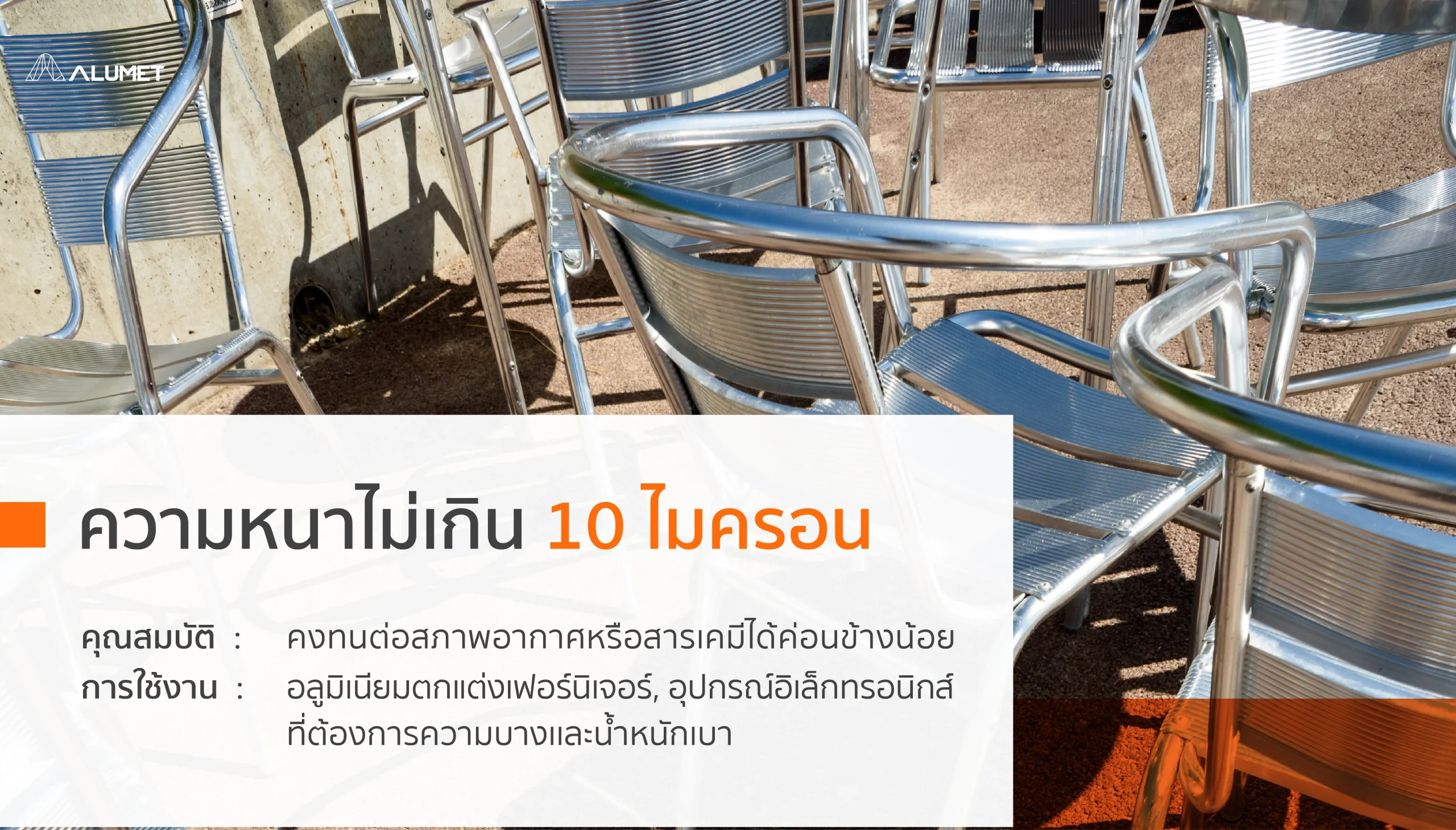
Oxide Thickness 10-25 Microns:
This level of anodizing is moderately thick, offering strong durability and resistance to corrosion and high temperatures. It is ideal for automotive parts or door and window frames.
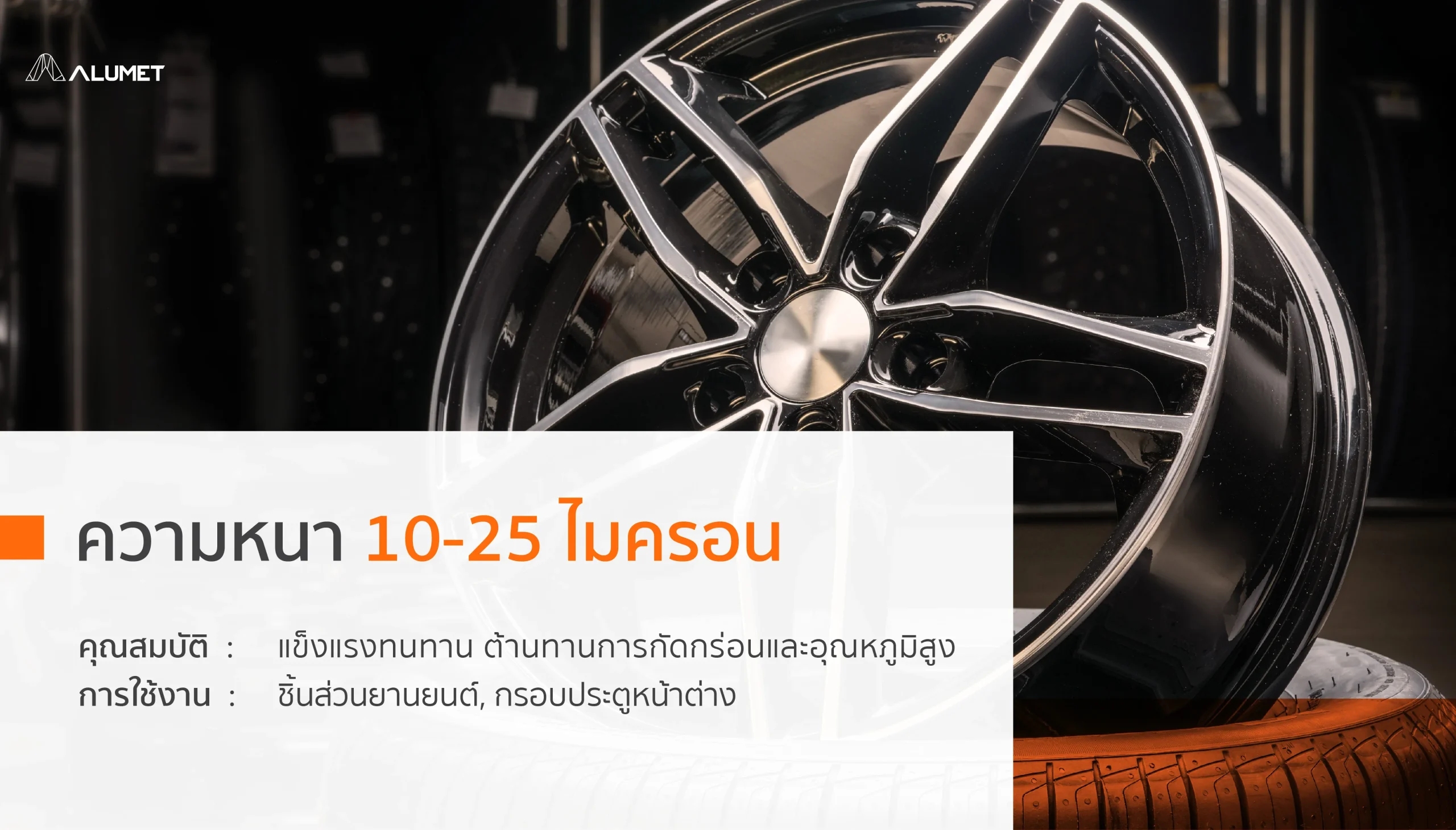
Oxide Thickness Over 25 Microns:
This is a high thickness level of anodized aluminium, providing excellent strength, high corrosion resistance, and long service life. It is commonly used in manufacturing machinery parts, industrial equipment, or workpieces requiring high strength and durability.
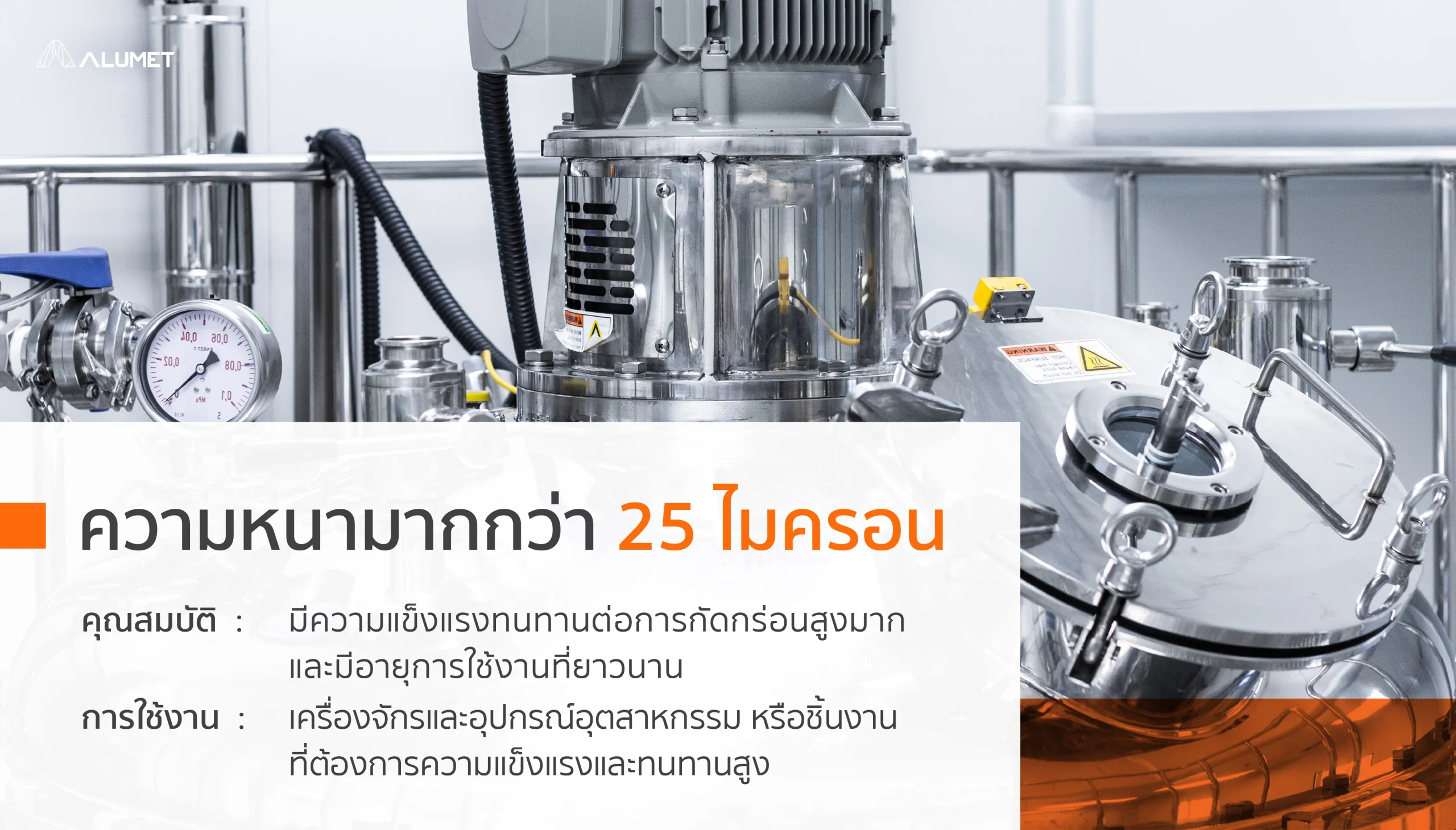
Alumet uses advanced computer-controlled anodizing processes and technology from Italy, allowing us to effectively manage and control parameters and variables affecting the workpiece. This ensures high-quality aluminium with consistently beautiful surface finish and color.
Reference sources:
https://metalfinishingsltd.co.uk/
https://www.bwcprofiles.co.uk/